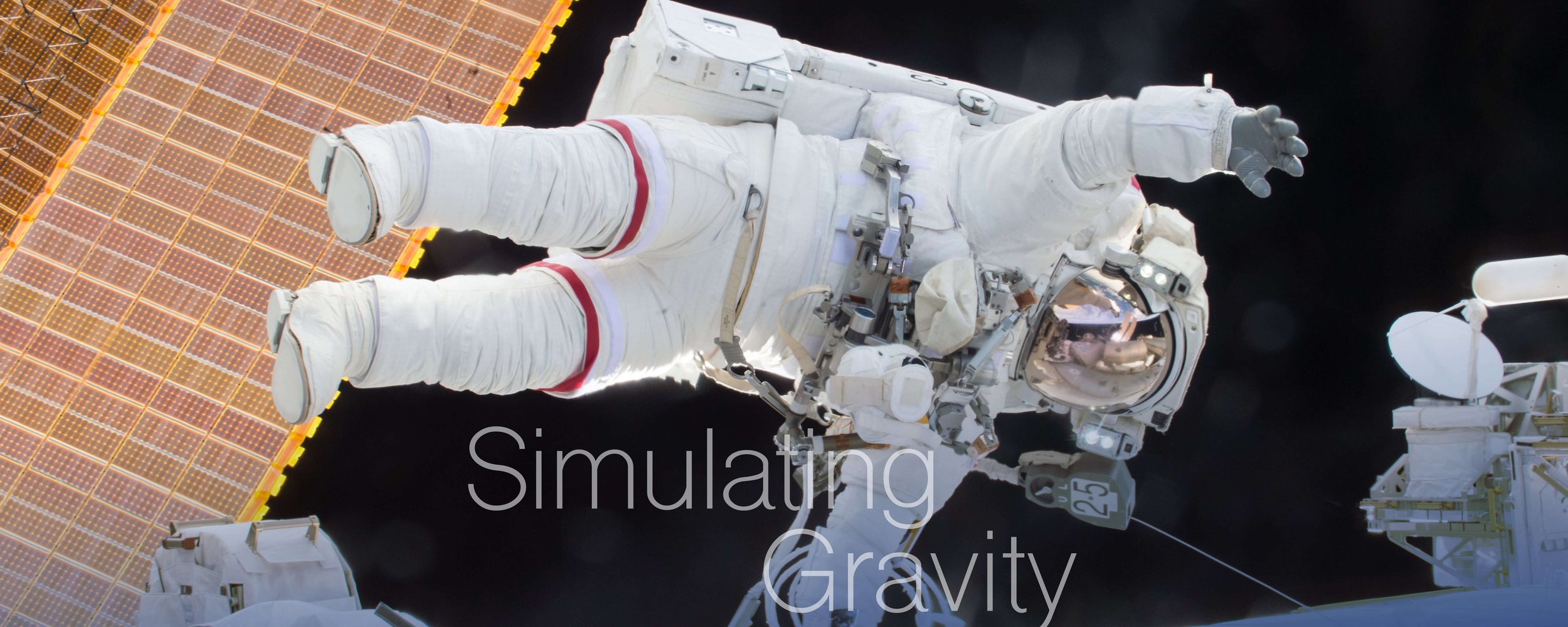
Simulating Gravity
Chris Quirk
On the morning of March 2, 2016, the Soyuz spacecraft carrying Commander Scott Kelly and cosmonaut Mikhail Kornienko descended from the International Space Station and bumped down on the Eurasian Steppes of central Kazakhstan. Kelly, who had been orbiting Earth for 340 days in the zero-gravity environment of the space station, was severely weakened after almost a year of floatingfreely in weightless conditions. The ground crew gingerly lifted the normally strapping Kelly out of the capsule and carried him to the nearby medical tent for testing.
Human beings suffer debilitating health effects when subject to zero-gravity settings for long periods, such as loss of bone mass, muscle atrophy and eyesight decline. In addition, astronauts can become temporarily delirious or confused immediately upon their return to Earth.
To counter these maladies and make long-term space exploration viable, NASA has a keen interest in finding ways to create gravity-like conditions in space. To that end, the space agency recently awarded a two-year, $600,000 grant to Zachary Manchester, assistant professor in the Robotics Institute, and his colleague, Jeffrey Lipton, assistant professor of mechanical engineering at the University of Washington, part of the NASA's Innovative Advanced Concepts program (NIAC). The researchers plan to design and deploy a folded structure large enough to simulate gravity in space. The idea being that the folded structure could be conveyed into space in a single launch. Once in orbit the structure would unfold to its much larger size, which combined with its ability to spin, would approximate Earth's gravity.
The challenge is formidable. The basic idea of using a spinning structure to create a centrifugal force that simulates gravity is not new. Anyone who has seen "2001: A Space Odyssey" will recall the sequence in which an astronaut is taking a leisurely jog, shadowboxing as he circumnavigates a track on the inside of the rotating spacecraft. If only it were as easy as it’s made to look in the film.
The central problem in simulating gravity in space by spinning is that humans begin to experience motion sickness at speeds of just two or three revolutions per minute. “That is really slow,” said Manchester. “In order to get near Earth’s gravity at around a 1.3 rpm range, you need a structure that is about a kilometer in length.”
Assembling a kilometer-long tower piece-by-piece in space would be a difficult enough task, but Manchester and Lipton plan to pack it into a single rocket.
“The classic way to do something like this is to fold it all up, like origami, into a really small space inside a rocket, then somehow deploy it,” Manchester said. “Right now, if you think about expansion ratios, the limits on what you can take up there and unfurl are around five or 10 times the original size. To get to a kilometer, you need to start with something about 10 meters in length and have an expansion ratio of 100-to-1.”
Flex structures for space would be retracted upon launch then extend and lock into place upon deployment.
To achieve such an extreme expansion ratio, Manchester and Lipton are combining scissor joints — similar to what you would see on a pair of expanding tongs — with a technique Lipton calls handed shearing auxetics, a slinky-like form that twists as it unscrews and expands in length.
“At one scale, you've got a scissor mechanism, and then that second structure that gives you another property,” Lipton said. “By combining the two into a hierarchical metamaterial, each operating on its own scale, we can get a much larger expansion ratio.” The materials and hinging apparatus on the space structure will be critical to the success of the project. Manchester and
Lipton are scouring the archives to find new or overlooked ideas for connecting the hundreds of thousands of pieces that will constitute the final structure. “It’s a deep literature search on all the different latching technologies out there and how we could apply them in a space context,” Lipton said.
As if these hurdles weren’t enough, the plan is to have a pod on each end of the kilometer-long arm large enough to house an astronaut. Naturally, there would be quite a bit of flex in the structure as it opens, and once it extends. As the structure deploys to its full length in space, with hundreds of thousands of joints opening and struts locking into place, plenty of things could go wrong. Manchester's idea is to use the natural flex in the elongated system to help ease the parts into order to avoid jamming.
“You’ve got to manufacture this thing, and nothing is perfect, so you are going to have these little issues all over the place,” he said. “At the end of the day, it’s got to have one degree of freedom. All these pieces have to come together in one specific way. But with enough flex and wiggle room, things will sort of nudge into place, the alignment issues should just be noise.”
“The vomit comet is a bucket list thing Jeff and I have, but we would squeeze a lot of experiments into those short, zero-gravity descents.”
(Right) James Burgess (HNZ 2017). a clinical neurosurgeon and master of medical management, submitted this image from inside the NASA “Vomit Comet” while working on a research project studying bleeding in low gravity, along with (left) Kate Meacham (E 2001), Ph.D. and research faculty in the Gereau Lab at Washington University, and an unidentified researcher (center).
At present, Manchester and Lipton are proceeding on parallel tracks while exchanging information frequently. The two have known each other since their undergraduate days at Cornell, where they also both earned their doctorates. Lipton is handling the mechanical and materials side of the project and Manchester is working on the computer modeling. “The math is super gnarly,” said Manchester. “You’ve got so many pieces, simulating several hundred thousand links. It's just huge. So, what we do is, where feasible, use fewer pieces, average out all those links, and simulate expanding in chunks. Then we look at the fully expanded structure to see vibration, flexibility and all that stuff.”
Despite the complexity of the project, the pair has made rapid progress. Lipton estimates they have already achieved about a 40-to-1 expansion ratio in their design. On the agenda at some point is a trip on a zero-gravity, parabolic airliner flight — popularly known as a vomit comet — to see how the apparatus responds in space-like conditions. “We'll be able to check it in various states of deployment and do local tests,” Lipton said. “We'll also have fully deployed sections and be able to do regional tests and see how they deal with the acceleration.” ■