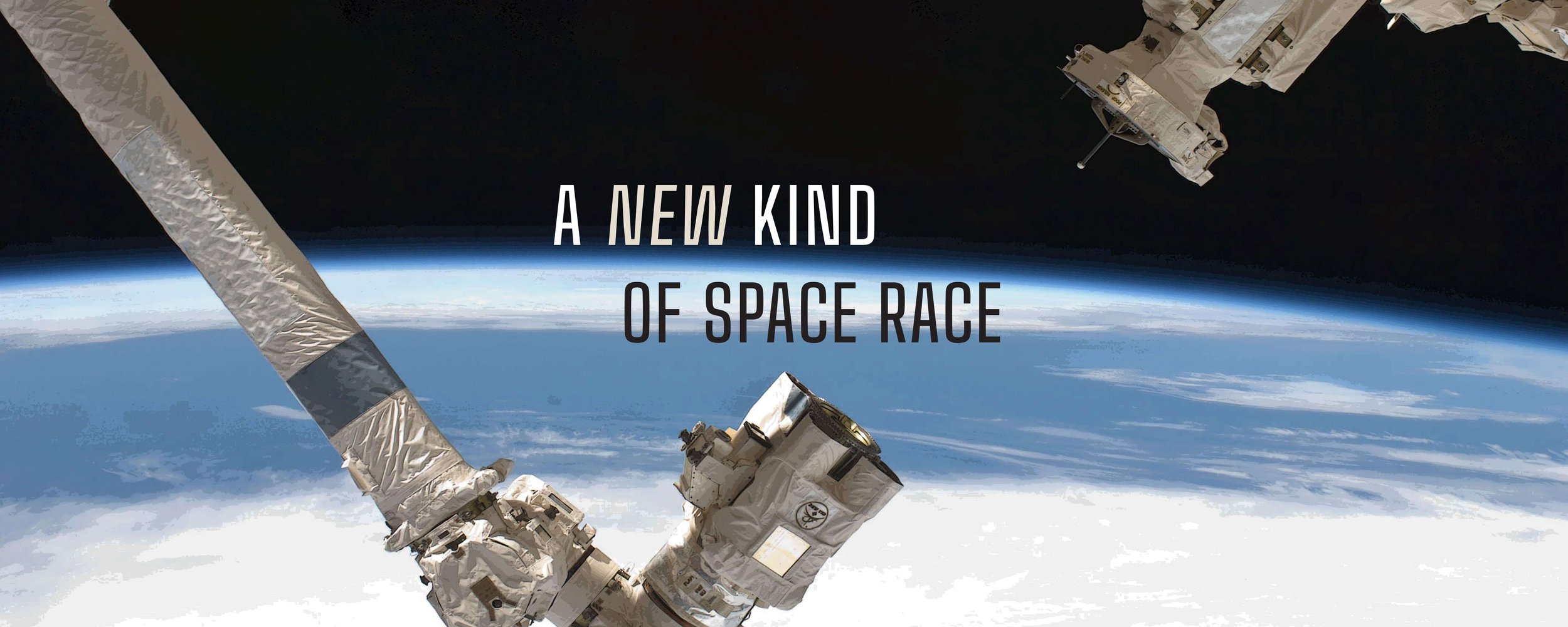
A New Kind of Space Race
Robotics Institute researchers partner with academia, industry to reduce space “junk”
Kayla Papakie
Think of the last time you put a key into a keyhole to unlock the door to your home or plugged a cord into an outlet to power up an electronic device. There’s a good chance you do small tasks like this every day, quickly and deftly, without even realizing you’re doing them.
Now imagine you're in space.
“Everything is spinning around at its own speed. You’re trying to put the key into your lock, but your house is moving, and you’re moving too,” said Howie Choset, the Kavcic-Moura Professor of Computer Science in the Robotics Institute.
These processes, known as peg-in-hole operations, are one of the many tasks essential to On-Orbit Servicing, Assembly and Manufacturing (OSAM), an emerging field where tools and technology are deployed to extend the lifespan of satellites. Peg-in-hole operations like unlocking a door or plugging in a phone charger are simple tasks we humans take for granted, but they aren't so easy for robots.
“People tend to really underestimate just how difficult these tasks are. They require a lot of precision and dexterity,” said Choset.
Choset and his team in the Biorobotics Lab study OSAM to explore ways in which robots can be put to use in space, particularly, how they can help to extend the lives of satellites.
Of the more than 6,300 satellites orbiting Earth, only half remain functional. Whether they’ve run out of fuel, malfunctioned or simply reached their intended lifespan, the disabled machinery is either guided to crash back into Earth's atmosphere and disintegrates upon re-entry or is pushed to an outer orbit – a satellite graveyard, of sorts – more than 200 miles away from any working spacecraft. These graveyards have come to be known as junk orbits, where more than 27,000 pieces of human-made space debris now float above the Earth.
To break this “launch once, use once” paradigm, Choset, along with Matt Travers, co-director of the Biorobotics Lab, and Carmel Majidi, a professor in CMU's College of Engineering, will lead a consortium as part of the Space University Research Initiative (SURI) out of the Air Force Research Laboratory and the Air Force Office of Scientific Research.
“If you could launch one rocket and have it serve multiple missions with that single launch, that is an absolute game changer in terms of efficiency and economy,” said Travers.
According to Choset, getting to that point is a big, multifaceted challenge. “A lot of different things have to come together to make this work,” he said.
Logistically, the team must consider how to build the robots before they deploy, how to launch them into space and how to control them once in orbit. Their research builds on previous work conducted by Choset and Travers with aerospace defense company Northrop Grumman that explored robotics and artificial intelligence for the company’s Mission Extension Vehicles.
“We’re hitting a point where there is commercial viability,” said Choset. “There’s money to be made here. Think of all those broken satellites. That’s trillions of dollars of hardware floating around.”
Howie Choset
Professor in Robotics Institute
Matt Travers
Co-director, Biorobotics Lab
Carmel Majidi
Professor in Mechanical Engineering
Space University Research Initiative
As part of the Space University Research Initiative, CMU will collaborate with researchers at the University of New Mexico, Texas A&M and the Northrop Grumman Corporation to develop systems for intelligent inspection, dexterous maintenance and agile manufacturing of satellites in space.
This three-way partnership among academia, government and industry brings together expertise in artificial intelligence, hard and soft robotics, additive manufacturing, astrodynamics, estimation theory, control and space systems.
Their proposal, ““Breaking the ‘Launch Once, Use Once’ Paradigm,” was one of two selected for the initiative. It is eligible for up to $1 million in funding per year, for three to five years.
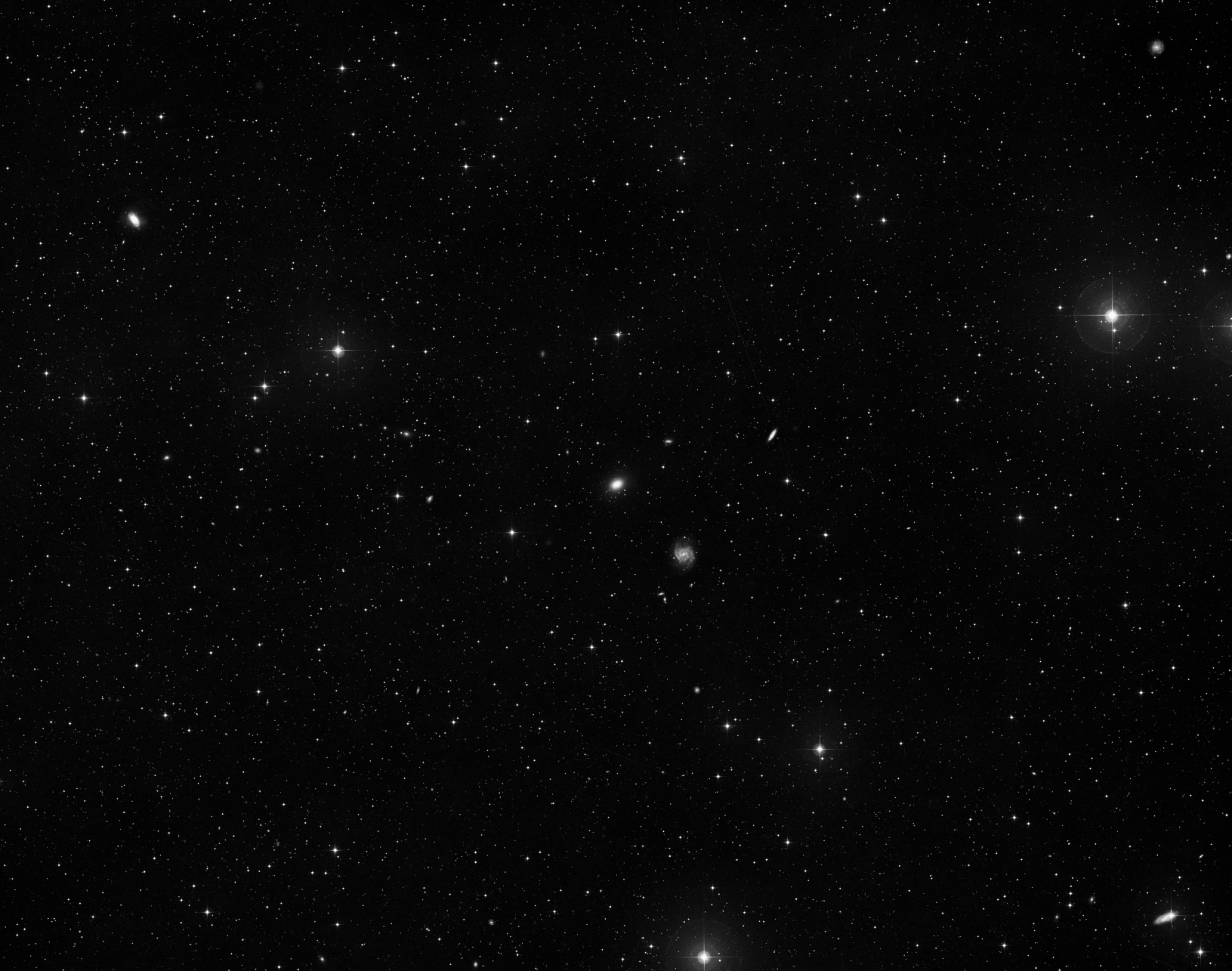
There are a number of ways in which this technology could help to prolong a satellite's usefulness.
“A satellite’s mission could dramatically change or there could be slight modifications where adding a sensor or adding a new rocket boost could completely renew its life cycle,” Travers said. “Bringing these capabilities to space makes a ton of sense.”
In addition to extending the lives of satellites in orbit, potential exists to lower the overhead costs of manufacturing and launching satellites by making them compact enough to be robotically assembled in space. Currently, satellites are carefully designed to be folded up and placed into the cargo bay of a space shuttle. They then have to withstand the pressure of being launched. Then once they're in space, they unfold and deploy.
“A lot of effort goes into building that satellite just so it could survive launch,” said Choset.
The Biorobotics Lab has a long history of building and deploying modular robots, and Choset believes this work, known as fixture-free manufacturing, can be transferred to satellites. The team is proposing modular satellites, with parts that can be packed up into small modules and then put together like Legos once in orbit.
Northrop Grumman has had early success with its Mission Extension Vehicles, the first of which docked on a client satellite in 2020. MEVs use their own thrusters and fuel supply to extend the satellite's lifespan. Once the satellite no longer needs servicing, the MEV can undock and move on to the next satellite in need. In 2021, the company's second MEV docked with an orbiting satellite.
CMU partnered with Northrop Grumman's subsidiary SpaceLogistics on this next generation of satellite life extension vehicles by assisting with vehicle dynamics in the company's Rendezvous, Proximity Operations and Docking Lab.
A Northrop Grumman Mission Robotic Vehicle uses its robotic arm to service a satellite in this rendering.
“Building robots that can fuel satellites or build new ones is not enough. We have to control these robots.”

At the root of the robotic servicing and assembling of satellites are fundamentals like control theory and robot manipulation.
“Building robots that can fuel satellites or build new ones is not enough. We have to control these robots,” said Choset. “You can't just tell the robot to go straight, because it's floating around in space.”
Control theory uses mathematics to predict and analyze system behavior, while robot manipulation refers to the ways in which a robot interacts with an object, like those ostensibly easy, but theoretically difficult peg-in-hole operations. These fundamental concepts present a framework for how to predict and guide robot movements as they complete tasks in space. However, these tasks could be complicated by anything from solar flares to gravity and momentum. What's more, a lag in communication from Earth to space further hinders such operations.
“That latency makes it very difficult to have a person on the ground with a joystick saying, ‘a little to the right, a little to the left’ because they'd make a move, and it takes a couple seconds for that message to get transmitted,” Travers said. By the time that command reaches the robot in space, it would already be in a different position than it was when the message was sent.
Considering the many moving parts to this research, Choset believes that few places are more equipped to handle such a complex venture.
“CMU is at a tipping point where, if we coagulate the efforts across our programs, I think we could be a space center,” said Choset. “There is an opportunity here for our university and our region to really have a coordinated impact in space.” ■